- 05 septembre 2019
- En Laurens Penninck
- | 6 min. temps de lecture
- | Source: Motion Control
VISION DE L'AVENIR AVEC L'IMPRESSION 3D
Materialise s'engage dans la numérisation et la production à la pointe de la technologie
Materialise n'est plus, depuis longtemps, un nom inconnu dans le monde de l'impression 3D. L'entreprise de Louvain se distingue en continuant à innover, seule ou avec des entreprises partenaires. Ces innovations ont conduit à l'attribution du 'Factory of the Future Award'. Materialise a été récompensé pour l'importance qu'il accorde à la numérisation, aux moyens de production les plus modernes et au développement de nouveaux produits et technologies.
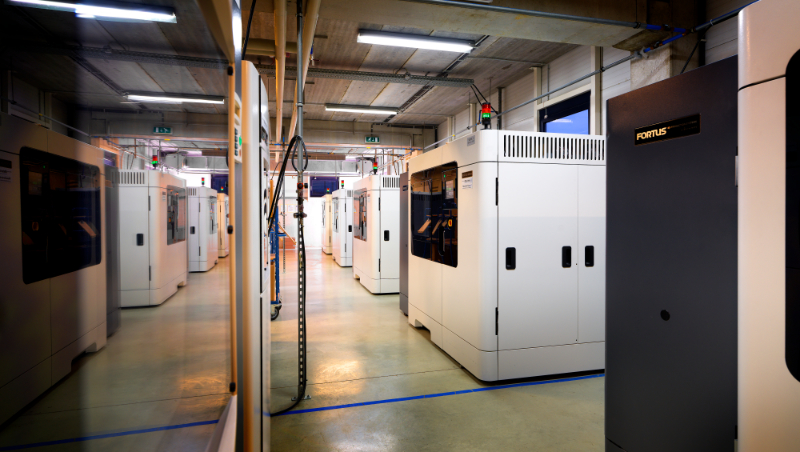
PIONNIER
Materialise fait autorité dans le monde de l'impression 3D depuis déjà près de trente ans. L'entreprise a été fondée en 1990 par Wilfried Vancraen et son épouse Hilde Ingelaere comme spin-off de la KU Leuven. Materialise a été l'un des pionniers de l'impression 3D et développe son savoir-faire depuis près de 30 ans. En 2014, l'entreprise s'est rendue à la bourse américaine NASDAQ pour acquérir plus de connaissances et de capital. Aujourd'hui, elle emploie plus de 2.000 personnes dans 19 pays différents.
"Nous imprimons pour deux grands groupes: le secteur médical - tout pour, dans ou sur le corps - et le secteur industriel", explique Bart Van der Schueren, CTO de Materialise.
REPARTITION DES ACTIVITES
Materialise divise ses activités d'impression en trois groupes.
La production unique
"D'abord, il y a la production unique. Il s'agit de la production de prototypes, y compris pour les voitures de course et les satellites", explique Van der Schueren.
La production en série
"Il y a aussi la production en série, qui est également courante chez Materialise. Ce sont par exemple des pièces pour avions ou pour drones." L'un des plus grands défis de l'impression 3D est de rendre l'activité financièrement attractive. L'Additive Manufacturing (AM) n'est pas élastique d'un point de vue prix. C'est pourquoi Materialise cherche des moyens pour réduire les coûts. "Par exemple, nous avons décidé de fabriquer des produits moins complexes, ce qui réduit également les coûts. Cela permet aussi d'augmenter la production en série."
Le sur mesure en masse
"Enfin, vous avez aussi la personnalisation de masse, la plus grande activité des trois. Les produits fabriqués ici sont liés à l'individu et sont souvent en rapport avec le médical, comme les prothèses auditives, les semelles intérieures ou les lunettes. Le déroulement du travail de l'orthèse est le suivant: un pied est placé sur une plaque de pression, après quoi un scan est effectué. Une analyse des données est ensuite effectuée. Sur la base de cette analyse, une conception est réalisée, qui est également vérifiée par des experts. Les deux dernières étapes sont l'impression et la livraison des semelles. Materialise produit env. 5.000 cas/produits médicaux uniques par mois." A côté des activités d'impression, Materialise développe également des logiciels pour l'impression 3D. Ils sont utilisés en interne, mais aussi vendus à d'autres acteurs de l'industrie. Une grande partie des imprimeries ne développent pas leur propre logiciel.
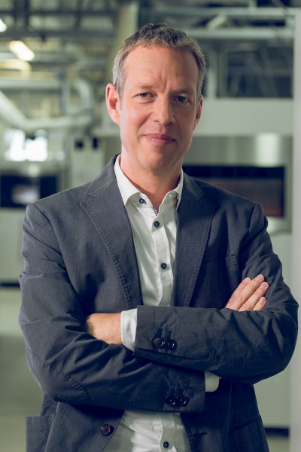
DIGITALISATION
Le cloud
Le cloud joue un rôle important chez Materialise. "Il vous permet de lier ou de partager des flux de processus, afin qu'ils puissent également être utilisés dans d'autres pays ou entreprises. Les plaques d'impression pour orthèses en sont un exemple. Celles-ci peuvent être déployées dans les magasins de sport. L'analyse peut entièrement être automatisée et effectuée par l'ordinateur. Après analyse, la conception peut aussi être automatisée. En répartissant les activités du cloud sur trois pays, espacés de huit heures chacun (Malaisie, Ukraine et Colombie), le cloud peut continuer à tourner et à fournir un service."
"La mise en relation de leurs compétences avec celles d'autres partenaires pour créer des applications de qualité est une valeur centrale"
Industrie 4.0
En mettant davantage l'accent sur la numérisation, on obtient une plus grande souplesse. Les imprimantes 3D doivent être connectées à l'espace de travail; le Build Processor a été développé à cet effet. C'est la technologie qui assure la communication entre le logiciel et les imprimantes 3D, réduisant ainsi la complexité de l'impression 3D. "A partir d'une plate-forme logicielle, vous pouvez connecter chaque imprimante au Build Processor. Cela vous permet d'établir des connexions avec le reste du système de production et d'établir une connexion avec le logiciel MES (Manufacturing Execution System). Il y a aussi le logiciel Magics Software - un logiciel polyvalent pour la préparation des données - et l'éditeur STL pour la fabrication d'additifs, qui permet de convertir des fichiers en STL, de réparer des erreurs, de modifier des dessins et de préparer des plates-formes de construction. Ainsi, on peut garder une trace de tout, parce que chaque machine a un identificateur de construction spécifique. Les lots peuvent y être liés afin de pouvoir voir à quelle distance les pièces se trouvent dans chaque construction. De plus, de plus en plus d'images de caméra sont utilisées pour obtenir de grosses données et avoir plus de contrôle du processus."
NETWORK FACTORY
La Network Factory est un autre critère pour l'attribution du FoF Award et fait partie de l'ADN de Materialise. La mise en relation de leurs compétences avec celles d'autres partenaires pour créer des applications de qualité est une valeur centrale.
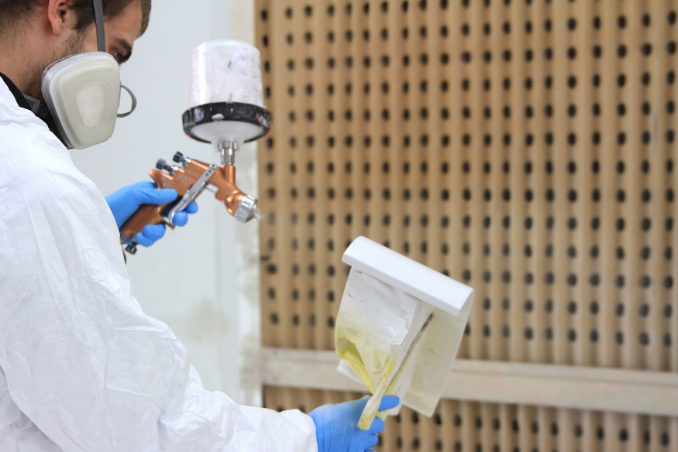
Le processus de pulvérisation se fait encore manuellement. A cette fin, le personnel suit des cours de formation intensifs.
Le post-traitement: le facteur humain est toujours très présent
Bien que Materialise s'engage fortement en faveur d'une plus grande numérisation dans les opérations de post-traitement, la plus grande partie de la numérisation se fait encore manuellement. "De nombreuses opérations doivent être effectuées, y compris la mesure et l'étiquetage des produits. Ceci se fait principalement manuellement. Une fois numérisé, il est plus facile de l'appliquer, mais aujourd'hui, nous avons toujours un important facteur humain." Materialise a investi dans la formation pour les pulvérisateurs afin de les pousser à un niveau supérieur.
WORLD CLASS PRODUCTION
L'un des critères pour l'attribution du FoF Award était le développement en interne de moyens de production de classe mondiale. C'est là que Materialise a engrangé des points. Peu après sa fondation, l'entreprise a commencé à fabriquer ses propres machines. Au début, il s'agissait de petites machines pour imprimer des modèles médicaux, comme des crânes. Ces imprimantes ont été développées pour devenir des 'imprimantes gigantesques' où l'on fabrique de grands modèles, des pare-chocs et des tableaux de bord.
Les vieilles imprimantes toujours actives
Les 'vieilles' imprimantes d'il y a 29 ans sont toujours utilisées chez Materialise. Elles reçoivent des mises à jour régulières: démontage complet et installation de nouveau matériel et construction de processeurs. Pendant toutes ces années, aucune machine n'a été jetée. La partie mécanique dure longtemps: un tel cadre peut durer au moins 30 ans. Cependant, l'optique nécessite beaucoup d'entretien, car le laser doit toujours avoir le bon diamètre. Sinon, vous aurez une perte de qualité.
A LA POINTE DE LA TECHNOLOGIE
Disposer d'installations de production ultramodernes est bien entendu également crucial pour la Factory of the Future. Materialise dispose donc d'imprimantes HP dotées des dernières technologies d'impression 3D. La plupart des machines et technologies utilisées par l'entreprise existent depuis relativement longtemps. "Un des projets que nous avons présentés, était lié au fait que l'impression 3D avec le procédé du lit de poudre fait souvent adhérer la poudre à la surface. L'excès de poudre qui y adhère, est sablé. La plus grande partie de cette matière est récupérée et recyclée. Avec la connaissance et l'impact de l'impression 3D de Materialise, une fraction résiduelle encore plus importante peut être récupérée pour une plus grande écoproduction."
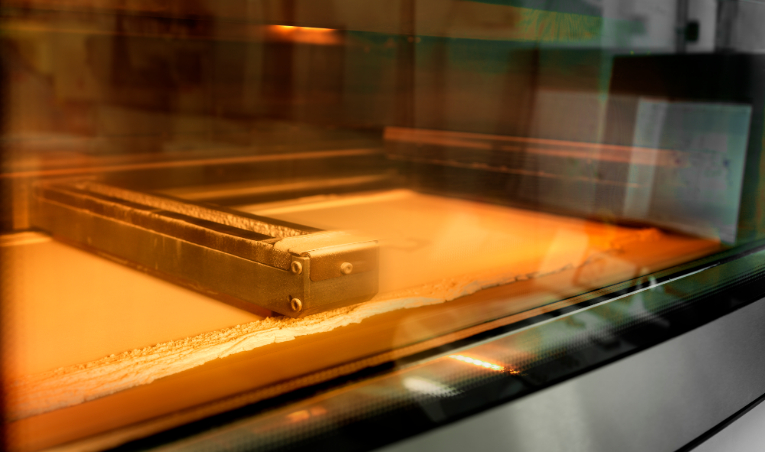
PRODUITS DE DESIGN
La plupart des activités de Materialise sont B2B, mais il y en a aussi qui sont B2C, comme les produits design. En 2004, les premiers pas ont été faits vers des produits finis avec impression 3D de lampes design. Toutefois, cela demeure une activité très concurrentielle. "Il existe une grande variété de produits et de matériaux. Le défi est d'offrir aux gens quelque chose qui leur permette de créer leur propre produit unique."
RAPIDFIT PLUS
RapidFit Plus est une filiale de Materialise issue du logiciel. "Il était souvent difficile d'envoyer des pare-chocs imprimés à l'étranger par le biais des services de livraison, car il y avait un risque de dommage. En réponse, une application a été développée qui supporte les profilés en aluminium avec une partie imprimée en 3D. Cette application a été développée afin de pouvoir effectuer des opérations de mesure pour des pièces de qualité. Ces activités ont continué à se développer, avec pour conséquence, la naissance de RapidFit - qui se concentre sur l'industrie automobile. Le fonctionnement? RapidFit/Materialise reçoit un plan de mesure du client avec un produit qu'il souhaite faire mesurer. Sur la base de ce plan, un produit est conçu, développé et construit. Le design a lieu à Kiev, l'assemblage et l'impression en Belgique. Les produits sont également mesurés avec les machines de mesure les plus récentes. L'impression elle-même n'est parfois pas assez précise, ce qui signifie que les produits sont souvent fraisés après l'impression.